Experimental and numerical study of MILD combustion in an open-end furnace with exhaust gas recirculation using methane and biogas
PhD Thesis
Title | Experimental and numerical study of MILD |
---|---|
Type | PhD Thesis |
Authors | |
Author | Noor, Muhamad Mat |
Supervisor | Wandel, Andrew P. |
Yusaf, Talal | |
Institution of Origin | University of Southern Queensland |
Qualification Name | Doctor of Philosophy |
Number of Pages | 310 |
Year | 2015 |
Abstract | The world's energy demand by 2042 is estimated at about 18 billion tons of oil equivalent with 80% fulfilled by the combustion of fossil fuel. Combustion is predicted In this study, an open-end furnace with an enclosure wall was used to capture the exhaust gas and utilised it as Exhaust Gas Recirculation (EGR). The EGR recirculates a portion of exhaust gas back to the combustion chamber to dilute the oxygen before the oxidant is mixed with the fuel and increases the reactant temperature. This setup is an open-end furnace because it allows a portion of The numerical modelling for the MILD combustion using CFD has been extensively conducted on different burners and different scale furnaces. In this study, the three-dimensional CFD model was utilised to develop and optimise the furnace. The Reynolds-Averaged Navier-Stokes (RANS) equations were solved using realisable k–ε turbulent models which has been shown by others to be a reasonably accurate model to predict the combustion temperatures and combustion The laboratory scale combustion chamber (total volume of 0.33 m3 and thermal ntensity of 18.8 kW/m3 atm) was developed and fabricated. In this study, the air and fuel supply system was also developed especially for this furnace operation. The parameters for the The numerical modelling for the partially-premixed methane and biogas using the same geometry and conditions as the experimental work is conducted and the flame temperatures are 1,499 K and 1,368 K respectively. These can be compared Further simulations were conducted using the same furnace geometry except a luff-body air-fuel nozzle to successfully achieve MILD combustion. The oxygen mole fraction is |
Keywords | moderate or intense low oxygen dilution combustion; open end furnace; MILD combustion; biogas; exhaust gas recirculation |
ANZSRC Field of Research 2020 | 401703. Energy generation, conversion and storage (excl. chemical and electrical) |
400402. Chemical and thermal processes in energy and combustion | |
401706. Numerical modelling and mechanical characterisation | |
Byline Affiliations | School of Mechanical and Electrical Engineering |
https://research.usq.edu.au/item/q3249/experimental-and-numerical-study-of-mild-combustion-in-an-open-end-furnace-with-exhaust-gas-recirculation-using-methane-and-biogas
Download files
2133
total views757
total downloads8
views this month0
downloads this month
Export as
Related outputs
The Simulation of Biogas Combustion in Top Open Burner
Selvam, A., Noor, M.M., Norhafana, M., Ihsan, C.K., Khalid, A., Mahmood, R.A., Harikrishnan, S. and Nayak, S.. 2024. "The Simulation of Biogas Combustion in Top Open Burner." 7th International Conference on Mechanical Engineering Research 2023 (ICMER 2023). Kuantan, Malaysia 12 - 13 Sep 2023 United Kingdom . IOP Publishing. https://doi.org/10.1088/1742-6596/2688/1/012023Review of mechanical vapour compression refrigeration system Part 2: performance challenge
Mahmood, R. A., Ali, O. M., Al-Janabi, A., Al-Doori, G. and Noor, M. M.. 2021. "Review of mechanical vapour compression refrigeration system Part 2: performance challenge." International Journal of Applied Mechanics and Engineering. 26 (3), pp. 119-130. https://doi.org/10.2478/ijame-2021-0039Mechanical Vapour Compression Refrigeration System: Review Part 1: Environment Challenge
Mahmood, Raid, Ali, Omar M. and Noor, M. M.. 2020. "Mechanical Vapour Compression Refrigeration System: Review Part 1: Environment Challenge." International Journal of Applied Mechanics and Engineering. 25 (4), pp. 130-147. https://doi.org/10.2478/ijame-2020-0054The study of air fuel ratio for open furnace MILD combustion of biogas on bluff-body burner
Noor, M. M., Wandel, Andrew P. and Yusaf, T. F.. 2012. "The study of air fuel ratio for open furnace MILD combustion of biogas on bluff-body burner." 2012 Southern Regional Engineering Conference (SREC 2012). Toowoomba, Australia 01 Sep 2012 Canberra, Australia.The development of MILD combustion open burner experimental setup
Noor, M. M., Wandel, Andrew P. and Yusaf, Talal. 2013. "The development of MILD combustion open burner experimental setup." Ishak, Mahadzir and Rahman, Md. Mustafizur (ed.) 2nd International Conference of Mechanical Engineering Research (ICMER 2013). Pahang, Malaysia 01 - 03 Jul 2013 Pahang, Malaysia.Detail guide for CFD on the simulation of biogas combustion in bluff-body mild burner
Noor, M. M., Wandel, Andrew P. and Yusaf, Talal. 2013. "Detail guide for CFD on the simulation of biogas combustion in bluff-body mild burner." Ishak, Mahadzir and Rahman, Md. Mustafizur (ed.) 2nd International Conference of Mechanical Engineering Research (ICMER 2013). Pahang, Malaysia 01 - 03 Jul 2013 Pahang, Malaysia.Mild combustion: the future for lean and clean combustion
Yusaf, Talal, Noor, M. M. and Wandel, Andrew P.. 2013. "Mild combustion: the future for lean and clean combustion." Ishak, Mahadzir and Rahman, Md. Mustafizur (ed.) 2nd International Conference of Mechanical Engineering Research (ICMER 2013). Pahang, Malaysia 01 - 03 Jul 2013 Pahang, Malaysia.Air fuel ratio study for mixture of biogas and hydrogen on mild combustion
Noor, M. M., Wandel, Andrew P. and Yusaf, Talal. 2014. "Air fuel ratio study for mixture of biogas and hydrogen on mild combustion." International Journal of Automotive and Mechanical Engineering. 10 (1), pp. 2144-2154. https://doi.org/10.15282/ijame.9.2013.29.0180Effect of air-fuel ratio on temperature distribution and pollutants for biogas MILD combustion
Noor, M. M., Wandel, Andrew P. and Yusaf, Talal. 2014. "Effect of air-fuel ratio on temperature distribution and pollutants for biogas MILD combustion." International Journal of Automotive and Mechanical Engineering. 10 (1), pp. 1980-1992. https://doi.org/10.15282/ijame.10.2014.15.0166The simulation of biogas combustion in a MILD burner
Noor, M. M., Wandel, Andrew P. and Yusaf, Talal. 2014. "The simulation of biogas combustion in a MILD burner." Journal of Mechanical Engineering and Sciences. 6 (1), pp. 995-1013.MILD combustion: the future for lean and clean combustion technology
Noor, M. M., Wandel, Andrew P. and Yusaf, Talal. 2014. "MILD combustion: the future for lean and clean combustion technology." International Review of Mechanical Engineering. 8 (1), pp. 251-257.Design and development of mild combustion burner
Noor, M. M., Wandel, Andrew P. and Yusaf, Talal. 2013. "Design and development of mild combustion burner." Journal of Mechanical Engineering and Sciences. 5, pp. 662-676. https://doi.org/10.15282/jmes.5.2013.13.0064Effect of compressed natural gas mixing on the engine performance and emissions
Yusaf, T., Baker, P., Hamawand, I. and Noor, M. M.. 2013. "Effect of compressed natural gas mixing on the engine performance and emissions." International Journal of Automotive and Mechanical Engineering. 8 (1), pp. 1416-1429.Analysis of recirculation zone and ignition position of non-premixed bluff-body for biogas mild combustion
Noor, M. M., Wandel, Andrew P. and Yusaf, Talal. 2013. "Analysis of recirculation zone and ignition position of non-premixed bluff-body for biogas mild combustion." International Journal of Automotive and Mechanical Engineering. 8 (1), pp. 1176-1186.The analysis of recirculation zone and ignition position of non-premixed bluff-body for biogas mild combustion
Noor, M. M., Wandel, Andrew P. and Yusaf, Talal. 2013. "The analysis of recirculation zone and ignition position of non-premixed bluff-body for biogas mild combustion." Ishak, Mahadzir and Rahman, Md. Mustafizur (ed.) 2nd International Conference of Mechanical Engineering Research (ICMER 2013). Pahang, Malaysia 01 - 03 Jul 2013 Pahang, Malaysia.Numerical study of oxygen dilution and temperature distribution of biogas combustion in Bluff-body MILD burner
Noor, M. M., Wandel, Andrew P. and Yusaf, Talal. 2013. "Numerical study of oxygen dilution and temperature distribution of biogas combustion in Bluff-body MILD burner." Masri, Assaad (ed.) 7th Australian Combustion Symposium (ACS 2013). Perth, Australia 06 - 08 Nov 2013 Perth, Australia.The air fuel ratio study for the mixture of biogas and hydrogen on mild combustion
Noor, M. M., Wandel, Andrew P. and Yusaf, Talal. 2013. "The air fuel ratio study for the mixture of biogas and hydrogen on mild combustion." 3rd Malaysian Postgraduate Conference (MPC 2013). Sydney, Australia 04 - 05 Jul 2013 Sydney, Australia.Discretization of three dimensional non-uniform grid: conditional moment closure elliptic equation using finite difference method
Noor, M. M., Wandel, Andrew P. and Yusaf, Talal. 2013. "Discretization of three dimensional non-uniform grid: conditional moment closure elliptic equation using finite difference method." 3rd Malaysian Postgraduate Conference (MPC 2013). Sydney, Australia 04 - 05 Jul 2013 Sydney, Australia.The potential of wind and solar energy in Malaysia east coast: preliminary study at Universiti Malaysia Pahang (UMP)
Amirruddin, A. K., Noor, M. M., Kadirgama, K. and Sharma, K. V.. 2012. "The potential of wind and solar energy in Malaysia east coast: preliminary study at Universiti Malaysia Pahang (UMP) ." Brebbia, C. A. and Zubir, S. S. (ed.) 3rd International Conference on Management of Natural Resources, Sustainable Development and Ecological Hazards: Ravage of the Planet III (RAV 2011) . Selangor, Malaysia 13 - 15 Dec 2011 Southampton, UK .A review of mild combustion and open furnace design consideration
Noor, M. M., Wandel, Andrew P. and Yusaf, Talal. 2012. "A review of mild combustion and open furnace design consideration." International Journal of Automotive and Mechanical Engineering. 6 (1), pp. 730-754.Investigation of Biogas Moderate or Intense Low Oxygen Dilution (MILD) combustion on open furnace bluff-body burner
Noor, M. M., Wandel, Andrew P. and Yusaf, T. F.. 2012. "Investigation of Biogas Moderate or Intense Low Oxygen Dilution (MILD) combustion on open furnace bluff-body burner." Noor, M. M., Baker, Paul and Yusaf, Talal F. (ed.) USQ Combustion Meeting 2012 (29th August). Toowoomba, Australia 29 Aug 2012 Toowoomba, Australia.Modelling of non-premixed turbulent combustion of hydrogen using conditional moment closure method
Noor, M. M., Hairuddin, A. Aziz, Wandel, Andrew P. and Yusaf, T. F.. 2012. "Modelling of non-premixed turbulent combustion of hydrogen using conditional moment closure method." IOP Conference Series: Materials Science and Engineering. 36 (1), pp. 1-17. https://doi.org/10.1088/1757-899X/36/1/012036The modelling of the effect of air fuel ratio on unburned hydrocarbons for MILD combustion
Noor, M. M., Wandel, Andrew P. and Yusaf, T. F.. 2012. "The modelling of the effect of air fuel ratio on unburned hydrocarbons for MILD combustion." Noor, M. M., Rahman, M. M. and Ismail, J. (ed.) 2nd Malaysian Postgraduate Conference (MPC 2012). Gold Coast, Australia 07 - 09 Jul 2012 Sydney, Australia.A preliminary study of control parameters for open furnace mild combustion using CFD
Noor, M. M., Wandel, Andrew P. and Yusaf, T. F.. 2012. "A preliminary study of control parameters for open furnace mild combustion using CFD." Noor, M. M., Rahman, M. M. and Ismail, J. (ed.) 2nd Malaysian Postgraduate Conference (MPC 2012). Gold Coast, Australia 07 - 09 Jul 2012 Sydney, Australia.Mild combustion: a technical review towards open furnace combustion
Noor, M. M., Wandel, Andrew P. and Yusaf, T. F.. 2012. "Mild combustion: a technical review towards open furnace combustion." Noor, M. M., Rahman, M. M. and Ismail, J. (ed.) 2nd Malaysian Postgraduate Conference (MPC 2012). Gold Coast, Australia 07 - 09 Jul 2012 Sydney, Australia.Numerical investigation of influence of air and fuel dilution for open furnace MILD combustion burner
Noor, M. M., Wandel, Andrew P. and Yusaf, T. F.. 2012. "Numerical investigation of influence of air and fuel dilution for open furnace MILD combustion burner." 2012 Southern Regional Engineering Conference (SREC 2012). Toowoomba, Australia 01 Sep 2012 Canberra, Australia.The potential of wind and solar energy in Malaysia east coast: preliminary study at Universiti Malaysia Pahang (UMP)
Noor, M. M., Amiruddin, A. K., Kadirgama, K. and Sharma, K. V.. 2011. "The potential of wind and solar energy in Malaysia east coast: preliminary study at Universiti Malaysia Pahang (UMP)." Brebbia, C. A. and Zubir, S. S. (ed.) 3rd International Conference on Energy and Sustainability . Alicante, Spain 11 - 13 Apr 2011 United Kingdom .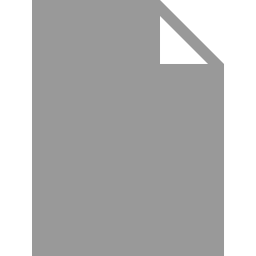