Transverse permeability of dry fiber preforms manufactured by automated fiber placement
Article
Article Title | Transverse permeability of dry fiber preforms manufactured by automated fiber placement |
---|---|
ERA Journal ID | 4884 |
Article Category | Article |
Authors | Aziz, A. R. (Author), Ali, M. A. (Author), Zeng, X. (Author), Umer, R. (Author), Schubel, P. (Author) and Cantwell, W. J. (Author) |
Journal Title | Composites Science and Technology |
Journal Citation | 152, pp. 57-67 |
Number of Pages | 11 |
Year | 2017 |
Publisher | Elsevier |
Place of Publication | United Kingdom |
ISSN | 0266-3538 |
1879-1050 | |
Digital Object Identifier (DOI) | https://doi.org/10.1016/j.compscitech.2017.09.011 |
Web Address (URL) | http://www.sciencedirect.com/science/article/pii/S026635381731610X |
Abstract | This work presents a correlation between the transverse permeability of a preform and the process variability of the automated dry fiber placement manufacturing technique. In this study, an experimental and numerical analysis of the dry tape preform, with a focus on its through-thickness permeability, has been undertaken. Geometric models, containing flow channels of two different width dry tape carbon preforms, have been created in the TexGen modeller. A Computational fluid dynamics (CFD) simulation has been undertaken to obtain the predicted through-thickness-permeability of the dry tape preform. A parametric study on the effect of different dry tape gap sizes on the permeability of the preform is presented. An in-situ compaction study, carried out in an X-CT machine, revealed that the gap sizes were irregular throughout the manufactured preforms. In addition, an experimental investigation of the through-thickness permeability, which is based on a saturated flow condition at a thickness corresponding to full vacuum pressure, is also presented. The permeability prediction based on the X-CT re-constructed geometric model has been validated using the experimental data. A further parametric study has revealed that the process variablity in automated dry fibre placement influences the through-thickness permeability by a factor of upto 5. |
Keywords | Modeling; Automated fiber placement; Layered structures; Resin flow |
ANZSRC Field of Research 2020 | 401602. Composite and hybrid materials |
400101. Aerospace materials | |
401706. Numerical modelling and mechanical characterisation | |
Institution of Origin | University of Southern Queensland |
Byline Affiliations | Khalifa University, United Arab Emirates |
Centre for Future Materials |
https://research.usq.edu.au/item/q46q8/transverse-permeability-of-dry-fiber-preforms-manufactured-by-automated-fiber-placement
Download files
1147
total views613
total downloads0
views this month0
downloads this month
Export as
Related outputs
Engineering amine-modified ammonium polyphosphate for enhancing flame retardancy and smoke suppression of vinyl ester resin
Chu, Tao, Lu, Yixia, Hou, Boyou, Zhou, Zhezhe, Yang, Qingshan, Guo, Yong, Jafari, Pooya, Mushtaq, Asim, Zeng, Xuesen, Huo, Siqi and Song, Pingan. 2025. "Engineering amine-modified ammonium polyphosphate for enhancing flame retardancy and smoke suppression of vinyl ester resin." Construction and Building Materials. 475. https://doi.org/10.1016/j.conbuildmat.2025.141174Converting waste poly(ethylene terephthalate) into hierarchical porous carbon towards a high-performance supercapacitor
Wang, Kaile, Li, Ruiyang, Zeng, Xuesen, Song, Pingan, Sun, Jisheng and Song, Rongjun. 2025. "Converting waste poly(ethylene terephthalate) into hierarchical porous carbon towards a high-performance supercapacitor." Journal of Materials Chemistry A. 13 (10), pp. 7381-7391. https://doi.org/10.1039/d4ta08522aNew prediction model for the screw pull-out strength of polymer composite railway sleepers
Yu, Peng, Manalo, Allan, Ferdous, Wahid, Salih, Choman, Abousnina, Rajab, Heyer, Tom and Schubel, Peter. 2024. "New prediction model for the screw pull-out strength of polymer composite railway sleepers." Construction and Building Materials. 433. https://doi.org/10.1016/j.conbuildmat.2024.136720Effects of through-thickness dielectric sensor on carbon fibre epoxy cure monitoring
Hall, Molly, Zeng, Xuesen, Shelley, Tristan and Schubel, Peter. 2024. "Effects of through-thickness dielectric sensor on carbon fibre epoxy cure monitoring." Composites Part A: Applied Science and Manufacturing. 182. https://doi.org/10.1016/j.compositesa.2024.108168Stochastic modelling of out-of-autoclave epoxy composite cure cycles under uncertainty
Hall, Molly, Zeng, Xuesen, Shelley, Tristan and Schubel, Peter. 2024. "Stochastic modelling of out-of-autoclave epoxy composite cure cycles under uncertainty." Composites Part A: Applied Science and Manufacturing. 180. https://doi.org/10.1016/j.compositesa.2024.108110Formation of non-uniform fibre distribution and its effect on the flexural performance of pultruded GFRP box beams
Qi, Songming, Alajarmeh, Omar, Alhawamdeh, Mohammad, Shelley, Tristan, Schubel, Peter, Rendle-Short, Kendric and Zeng, Xuesen. 2024. "Formation of non-uniform fibre distribution and its effect on the flexural performance of pultruded GFRP box beams." Composite Structures. 327. https://doi.org/10.1016/j.compstruct.2023.117695Finite element analysis and experimental validation of polymer–metal contacts in block-on-ring configuration
Awwad, K. Y. Eayal, Fallahnezhad, Khosro, Yousif, B. F., Mostafa, Ahmad, Alajarmeh, Omar, Shalwan, A. and Zeng, Xuesen. 2024. "Finite element analysis and experimental validation of polymer–metal contacts in block-on-ring configuration." Friction. 12 (3), pp. 554-568. https://doi.org/10.1007/s40544-023-0795-xDielectric parameter independent curing analysis of out-of-autoclave carbon fibre/epoxy composites
Hall, Molly, Zeng, Xuesen, Shelley, Tristan and Schubel, Peter. 2023. "Dielectric parameter independent curing analysis of out-of-autoclave carbon fibre/epoxy composites." Composites Part A: Applied Science and Manufacturing. 175. https://doi.org/10.1016/j.compositesa.2023.107755Characterisation of Curing of Vinyl Ester Resin in an Industrial Pultrusion Process: Influence of Die Temperature
Chaparala, Sai Ajay Chandra, Alajarmeh, Omar, Shelley, Tristan, Zeng, Xuesen, Rendle-Short, Kendric, Voice, Dean and Schubel, Peter. 2023. "Characterisation of Curing of Vinyl Ester Resin in an Industrial Pultrusion Process: Influence of Die Temperature." Polymers. 15 (18). https://doi.org/10.3390/polym15183808Fatigue behavior of unidirectional fiber-reinforced pultruded composites with high volume fiber fraction
Alajarmeh, Omar, Manalo, Allan, Ferdous, Wahid, Almasabha, Ghassan, Tarawneh, Ahmad, Awwad, Khaled Eayal, Safonov, Alexander, Zeng, Xuesen and Schubel, Peter. 2023. "Fatigue behavior of unidirectional fiber-reinforced pultruded composites with high volume fiber fraction." Fatigue and Fracture of Engineering Materials and Structures. 46 (6), pp. 2034-2048. https://doi.org/10.1111/ffe.13979Formation of non-uniform fibre distributions in winding-pultrusion process and its effect on axial compressive properties of hollow GFRP profiles
Qi, Songming, Alajarmeh, Omar, Shelley, Tristan, Schubel, Peter, Rendle-Short, Kendric and Zeng, Xuesen. 2023. "Formation of non-uniform fibre distributions in winding-pultrusion process and its effect on axial compressive properties of hollow GFRP profiles ." Composites Part A: Applied Science and Manufacturing. 173. https://doi.org/10.1016/j.compositesa.2023.107659A Schiff base-coated ammonia polyphosphate for improving thermal and fire-retardant properties of unsaturated polyester
Zhang, Jianzhong, Fang, Yang, Zhang, Anlin, Yu, Youming, Liu, Lina, Huo, Siqi, Zeng, Xuesen, Peng, Hong and Song, Pingan. 2023. "A Schiff base-coated ammonia polyphosphate for improving thermal and fire-retardant properties of unsaturated polyester." Progress in Organic Coatings. 185. https://doi.org/10.1016/j.porgcoat.2023.107910Engineering phosphorus-containing lignin for epoxy biocomposites with enhanced thermal stability, fire retardancy and mechanical properties
Zhang, Anlin, Zhang, Jianzhong, Liu, Lina, Dai, Jinfeng, Lu, Xinyu, Huo, Siqi, Hong, Min, Liu, Xiaohuan, Lynch, Mark, Zeng, Xuesen, Burey, Paulomi and Song, Pingan. 2023. "Engineering phosphorus-containing lignin for epoxy biocomposites with enhanced thermal stability, fire retardancy and mechanical properties." Journal of Materials Science and Technology. 167, pp. 82-93. https://doi.org/10.1016/j.jmst.2023.06.004An iron phenylphosphinate@graphene oxide nanohybrid enabled flame-retardant, mechanically reinforced, and thermally conductive epoxy nanocomposites
Chen, Qiang, Liu, Lei, Zhang, Anlin, Wang, Wenduo, Wang, Zhengzhou, Zhang, Jianzhong, Feng, Jiabing, Huo, Siqi, Zeng, Xuesen and Song, Pingan. 2023. "An iron phenylphosphinate@graphene oxide nanohybrid enabled flame-retardant, mechanically reinforced, and thermally conductive epoxy nanocomposites." Chemical Engineering Journal. 454. https://doi.org/10.1016/j.cej.2022.140424Tribological and mechanical performances of newly developed eco-epoxy composites incorporating flax fibres and graphene nanoplatelets
Awwad, KY Eayal, Yousif, BF, Mostafa, Ahmad, Alajarmeh, Omar and Zeng, Xuesen. 2023. "Tribological and mechanical performances of newly developed eco-epoxy composites incorporating flax fibres and graphene nanoplatelets." Journal of Reinforced Plastics and Composites. 42 (17-18), p. 939–952. https://doi.org/10.1177/07316844221143451Fibre waviness characterisation and modelling by Filtered Canny Misalignment Analysis (FCMA)
Alajarmeh, Omar, Qi, Songming, Shelley, Tristan, Schubel, Peter, Rendle-Short, Kendric and Zeng, Xuesen. 2023. "Fibre waviness characterisation and modelling by Filtered Canny Misalignment Analysis (FCMA)." Composite Structures. 307. https://doi.org/10.1016/j.compstruct.2023.116666Design optimisation of hollow box pultruded FRP profiles using mixed integer constrained Genetic algorithm
Alhawamdeh, Mohammad, Alajarmeh, Omar, Aravinthan, Thiru, Shelley, Tristan, Schubel, Peter, Mohammed, Ali and Zeng, Xuesen. 2022. "Design optimisation of hollow box pultruded FRP profiles using mixed integer constrained Genetic algorithm." Composite Structures. 302, pp. 1-21. https://doi.org/10.1016/j.compstruct.2022.116247In situ Thermoset Cure Sensing: A Review of Correlation Methods
Hall, Molly, Zeng, Xuesen, Shelley, Tristan and Schubel, Peter. 2022. "In situ Thermoset Cure Sensing: A Review of Correlation Methods." Polymers. 14 (15), pp. 1-29. https://doi.org/10.3390/polym14152978Screw lateral restraint behaviour of timber and polymeric based railway sleepers
Yu, Peng, Manalo, Allan, Ferdous, Wahid, Salih, Choman, Heyer, Tom and Schubel, Peter. 2022. "Screw lateral restraint behaviour of timber and polymeric based railway sleepers." Engineering Failure Analysis. 139, pp. 1-18. https://doi.org/10.1016/j.engfailanal.2022.106514Influence of post-processing on the compressive behaviour of full-scale pultruded FRP columns: Holes and inserts
Alajarmeh, Omar, Alhawamdeh, Mohammad, Shelley, Tristan, Mohammed, Ali, Nicol, Lachlan, Schubel, Peter and Zeng, Xuesen. 2022. "Influence of post-processing on the compressive behaviour of full-scale pultruded FRP columns: Holes and inserts." Engineering Structures. 266, pp. 1-16. https://doi.org/10.1016/j.engstruct.2022.114547Novel Bending Test Method for Polymer Railway Sleeper Materials
Salih, Choman, Manalo, Allan, Ferdous, Wahid, Abousnina, Rajab, Yu, Peng, Heyer, Tom and Schubel, Peter. 2021. "Novel Bending Test Method for Polymer Railway Sleeper Materials." Polymers. 13 (9), pp. 1-22. https://doi.org/10.3390/polym13091359Behaviour of timber-alternative railway sleeper materials under five-point bending
Salih, Choman, Manalo, Allan, Ferdous, Wahid, Yu, Peng, Heyer, Tom and Schubel, Peter. 2022. "Behaviour of timber-alternative railway sleeper materials under five-point bending." Construction and Building Materials. 316, pp. 1-12. https://doi.org/10.1016/j.conbuildmat.2021.125882Behaviour of Polymer Filled Composites for Novel Polymer Railway Sleepers
Ferdous, Wahid, Manalo, Allan, Salih, Choman, Yu, Peng, Abousnina, Rajab, Heyer, Tom and Schubel, Peter. 2021. "Behaviour of Polymer Filled Composites for Novel Polymer Railway Sleepers." Polymers. 13 (8), pp. 1-13. https://doi.org/10.3390/polym13081324Bending and Shear Behaviour of Waste Rubber Concrete-Filled FRP Tubes with External Flanges
Ferdous, Wahid, Manalo, Allan, Alajarmeh, Omar S., Zhuge, Yan, Mohammed, Ali A., Bai, Yu, Aravinthan, Thiru and Schubel, Peter. 2021. "Bending and Shear Behaviour of Waste Rubber Concrete-Filled FRP Tubes with External Flanges." Polymers. 13 (15), pp. 1-18. https://doi.org/10.3390/polym13152500Effect of bending and compressive modulus of elasticity on the behaviour of timber-alternative railway sleepers supported by ballast
Salih, Choman, Manalo, Allan, Ferdous, Wahid, Yu, Peng, Abousnina, Rajab, Heyer, Tom and Schubel, Peter. 2021. "Effect of bending and compressive modulus of elasticity on the behaviour of timber-alternative railway sleepers supported by ballast." Case Studies in Construction Materials. 15, pp. 1-14. https://doi.org/10.1016/j.cscm.2021.e00597Investigation on the physical, mechanical and microstructural properties of epoxy polymer matrix with crumb rubber and short fibres for composite railway sleepers
Yu, Peng, Manalo, Allan, Ferdous, Wahid, Abousnina, Rajab, Salih, Choman, Heyer, Tom and Schubel, Peter. 2021. "Investigation on the physical, mechanical and microstructural properties of epoxy polymer matrix with crumb rubber and short fibres for composite railway sleepers." Construction and Building Materials. 295, pp. 1-14. https://doi.org/10.1016/j.conbuildmat.2021.123700Failure analysis and the effect of material properties on the screw pull-out behaviour of polymer composite sleeper materials
Yu, Peng, Manalo, Allan, Ferdous, Wahid, Salih, Choman, Abousnina, Rajab, Heyer, Tom and Schubel, Peter. 2021. "Failure analysis and the effect of material properties on the screw pull-out behaviour of polymer composite sleeper materials." Engineering Failure Analysis. 128, pp. 1-14. https://doi.org/10.1016/j.engfailanal.2021.105577Review on Local Buckling of Hollow Box FRP Profiles in Civil Structural Applications
Alhawamdeh, Mohammad, Alajarmeh, Omar, Aravinthan, Thiru, Shelley, Tristan, Schubel, Peter, Mohammed, Ali and Zeng, Xuesen. 2021. "Review on Local Buckling of Hollow Box FRP Profiles in Civil Structural Applications." Polymers. 13 (23), pp. 1-27. https://doi.org/10.3390/polym13234159Compression behavior of GFRP bars under elevated In-Service temperatures
Alajarmeh, Omar, Manalo, Allan, Benmokrane, Brahim, Schubel, Peter, Zeng, Xuesen, Ahmad, Afaq, Hassanli, Reza and Sorbello, Charles-Dean. 2022. "Compression behavior of GFRP bars under elevated In-Service temperatures." Construction and Building Materials. 314 (Part A). https://doi.org/10.1016/j.conbuildmat.2021.125675Modelling flexural performance of hollow pultruded FRP profiles
Alhawamdeh, Mohammad, Alajarmeh, Omar, Aravinthan, Thiru, Shelley, Tristan, Schubel, Peter, Mohammad, Ali and Zeng, Xuesen. 2021. "Modelling flexural performance of hollow pultruded FRP profiles." Composite Structures. 276. https://doi.org/10.1016/j.compstruct.2021.114553Recycling of landfill wastes (tyres, plastics and glass) in construction – A review on global waste generation, performance, application and future opportunities
Ferdous, Wahid, Manalo, Allan, Siddique, Rafat, Mendis, Priyan, Zhuge, Yan, Wong, Hong S., Lokuge, Weena, Aravinthan, Thiru and Schubel, Peter. 2021. "Recycling of landfill wastes (tyres, plastics and glass) in construction – A review on global waste generation, performance, application and future opportunities." Resources, Conservation and Recycling. 173, pp. 1-13. https://doi.org/10.1016/j.resconrec.2021.105745Modelling hollow pultruded FRP profiles under axial compression: Local buckling and progressive failure
Alhawamdeh, Mohammad, Alajarmeh, Omar, Aravinthan, Thiru, Shelley, Tristan, Schubel, Peter, Kemp, Michael and Zeng, Xuesen. 2021. "Modelling hollow pultruded FRP profiles under axial compression: Local buckling and progressive failure." Composite Structures. 262, pp. 1-14. https://doi.org/10.1016/j.compstruct.2021.113650Tensile Fatigue Behavior of Polyester and Vinyl Ester Based GFRP Laminates—A Comparative Evaluation
Ferdous, Wahid, Manalo, Allan, Yu, Peng, Salih, Choman, Abousnina, Rajab, Heyer, Tom and Schubel, Peter. 2021. "Tensile Fatigue Behavior of Polyester and Vinyl Ester Based GFRP Laminates—A Comparative Evaluation." Polymers. 13 (3), pp. 1-10. https://doi.org/10.3390/polym13030386Behaviour of continuous fibre composite sandwich core under low-velocity impact
Zangana, Sartip, Epaarachchi, Jayantha, Ferdous, Wahid, Leng, Jinsong and Schubel, Peter. 2021. "Behaviour of continuous fibre composite sandwich core under low-velocity impact." Thin-Walled Structures. 158, pp. 1-11. https://doi.org/10.1016/j.tws.2020.107157Self-healing polymers: Synthesis methods and applications
Reddy, Kakarla Raghava, El-Zein, Abbas, Airey, David W., Alonso-Marroquin, Fernando, Schubel, Peter and Manalo, Allan. 2020. "Self-healing polymers: Synthesis methods and applications." Nano-Structures and Nano-Objects. 23, pp. 1-21. https://doi.org/10.1016/j.nanoso.2020.100500Static behaviour of glass fibre reinforced novel composite sleepers for mainline railway track
Ferdous, Wahid, Manalo, Allan, Alajarmeh, Omar, Mohammed, Ali A., Salih, Choman, Yu, Peng, Mehrinejad Khotbehsara, Mojdeh and Schubel, Peter. 2021. "Static behaviour of glass fibre reinforced novel composite sleepers for mainline railway track." Engineering Structures. 229, pp. 1-11. https://doi.org/10.1016/j.engstruct.2020.111627Compressive behaviour of hollow box pultruded FRP columns with continuous-wound fibres
Alajarmeh, Omar, Zeng, Xuesen, Aravinthan, Thiru, Shelley, Tristan, Alhawamdeh, Mohammad, Mohammed, Ali, Nicol, Lachlan, Vedernikov, Alexander, Safonov, Alexander and Schubel, Peter. 2021. "Compressive behaviour of hollow box pultruded FRP columns with continuous-wound fibres." Thin-Walled Structures. 168. https://doi.org/10.1016/j.tws.2021.108300Through-thickness permeability of woven fabric under increasing air pressure: theoretical framework and simulation
Xiao, Xueliang, Long, Andrew, Qian, Kun, Zeng, Xuesen and Hua, Tao. 2017. "Through-thickness permeability of woven fabric under increasing air pressure: theoretical framework and simulation." Textile Research Journal. 87 (13), pp. 1631-1642. https://doi.org/10.1177/0040517516657062Influence of Graphene Nanoplatelets on Mechanical Properties and Adhesive Wear Performance of Epoxy-Based Composites
Eayal Awwad, K. Y., Yousif, B. F., Fallahnezhad, Khosro, Saleh, Khalid and Zeng, Xuesen. 2021. "Influence of Graphene Nanoplatelets on Mechanical Properties and Adhesive Wear Performance of Epoxy-Based Composites." Friction. 9 (4), pp. 856-875. https://doi.org/10.1007/s40544-020-0453-5Effect of fibre architecture on tensile pull-off behaviour of 3D woven composite T-joints
Yan, Shibo, Zeng, Xuesen and Long, Andrew. 2020. "Effect of fibre architecture on tensile pull-off behaviour of 3D woven composite T-joints." Composite Structures. 242, pp. 1-9. https://doi.org/10.1016/j.compstruct.2020.112194Testing and modelling the fatigue behaviour of GFRP composites – Effect of stress level, stress concentration and frequency
Ferdous, Wahid, Manalo, Allan, Peauril, Joshua, Salih, Choman, Reddy, Kakarla Raghava, Yu, Peng, Schubel, Peter and Heyer, Tom. 2020. "Testing and modelling the fatigue behaviour of GFRP composites – Effect of stress level, stress concentration and frequency." Engineering Science and Technology, an International Journal. 23 (5), pp. 1223-1232. https://doi.org/10.1016/j.jestch.2020.01.001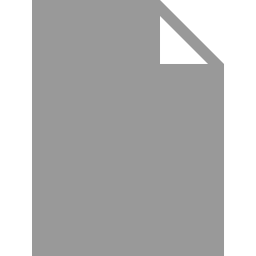